Preparation and characteristics of polyurethane semi-rigid foam for high-performance automotive handrails.
The armrest in the interior of the car is an important part of the cab, which plays the role of pushing and pulling the door and placing the arm of the person in the car. In the event of an emergency, when the car and the handrail collision, polyurethane soft handrail and modified PP (polypropylene), ABS (polyacrylonitrile - butadiene - styrene) and other hard plastic handrail, can provide good elasticity and buffer, thereby reducing injury. Polyurethane soft foam handrails can provide good hand feel and beautiful surface texture, thereby improving the comfort and beauty of the cockpit. Therefore, with the development of the automotive industry and the improvement of people's requirements for interior materials, the advantages of polyurethane soft foam in automotive handrails are becoming more and more obvious.
There are three kinds of polyurethane soft handrails: high resilience foam, self-crusted foam and semi-rigid foam. The outer surface of the high resilience handrails is covered with PVC (polyvinyl chloride) skin, and the interior is polyurethane high resilience foam. The support of the foam is relatively weak, the strength is relatively low, and the adhesion between the foam and the skin is relatively insufficient. The self-skinned handrail has a foam core layer of skin, low cost, high integration degree, and is widely used in commercial vehicles, but it is difficult to take into account the strength of the surface and the overall comfort. Semi-rigid armrest is covered with PVC skin, the skin provides good touch and appearance, and the internal semi-rigid foam has excellent feel, impact resistance, energy absorption and aging resistance, so it is more and more widely used in the use of passenger car interior.
In this paper, the basic formula of polyurethane semi-rigid foam for automobile handrails is designed, and its improvement is studied on this basis.
Experimental section
Main raw material
Polyether polyol A (hydroxyl value 30 ~ 40 mg/g), polymer polyol B (hydroxyl value 25 ~ 30 mg/g) : Wanhua Chemical Group Co., LTD. Modified MDI [diphenylmethane diisocyanate, w (NCO) is 25%~30%], composite catalyst, wetting dispersant (Agent 3), antioxidant A: Wanhua Chemical (Beijing) Co., LTD., Maitou, etc.; Wetting dispersant (Agent 1), wetting dispersant (Agent 2) : Byke Chemical. The above raw materials are industrial grade. PVC lining skin: Changshu Ruihua.
Main equipment and instruments
Sdf-400 type high-speed mixer, AR3202CN type electronic balance, aluminum mold (10cm×10cm×1cm, 10cm×10cm×5cm), 101-4AB type electric blower oven, KJ-1065 type electronic universal tension machine, 501A type super thermostat.
Preparation of basic formula and sample
The basic formulation of semi-rigid polyurethane foam is shown in Table 1.
Preparation of the mechanical properties test sample: the composite polyether (A material) was prepared according to the design formula, mixed with the modified MDI in a certain proportion, stirred with a high-speed stirring device (3000r/min) for 3~5s, then poured into the corresponding mold to foam, and opened the mold within a certain time to obtain the semi-rigid polyurethane foam molded sample.
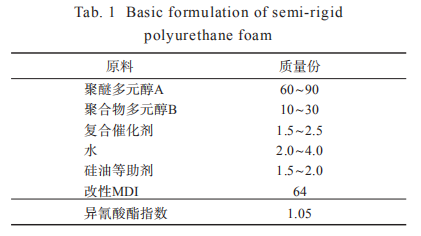
Preparation of the sample for bonding performance test: a layer of PVC skin is placed in the lower die of the mold, and the combined polyether and modified MDI are mixed in proportion, stirred by a high-speed stirring device (3 000 r/min) for 3~5 s, then poured into the surface of the skin, and the mold is closed, and the polyurethane foam with the skin is moulded within a certain time.
Performance test
Mechanical properties: 40%CLD (compressive hardness) according to ISO-3386 standard test; Tensile strength and elongation at break are tested according to ISO-1798 standard; Tear strength is tested according to ISO-8067 standard. Bonding performance: The electronic universal tension machine is used to peel the skin and foam 180° according to the standard of an OEM.
Aging performance: Test the loss of mechanical properties and bonding properties after 24 hours of aging at 120℃ according to the standard temperature of an OEM.
Results and discussion
Mechanical property
By changing the ratio of polyether polyol A and polymer polyol B in the basic formula, the influence of different polyether dosage on the mechanical properties of semi-rigid polyurethane foam was explored, as shown in Table 2.

It can be seen from the results in Table 2 that the ratio of polyether polyol A to polymer polyol B has a significant effect on the mechanical properties of polyurethane foam. When the ratio of polyether polyol A to polymer polyol B increases, the elongation at break increases, the compressive hardness decreases to a certain extent, and the tensile strength and tearing strength change little. The molecular chain of polyurethane mainly consists of soft segment and hard segment, soft segment from polyol and hard segment from carbamate bond. On the one hand, the relative molecular weight and hydroxyl value of the two polyols are different, on the other hand, the polymer polyol B is a polyether polyol modified by acrylonitrile and styrene, and the rigidity of the chain segment is improved due to the existence of benzene ring, while the polymer polyol B contains small molecular substances, which increases the brittleness of the foam. When polyether polyol A is 80 parts and polymer polyol B is 10 parts, the comprehensive mechanical properties of the foam are better.
Bonding property
As a product with high press frequency, the handrail will significantly reduce the comfort of parts if the foam and skin peel, so the bonding performance of polyurethane foam and skin is required. On the basis of the above research, different wetting dispersants were added to test the adhesion properties of the foam and the skin. The results are shown in Table 3.

It can be seen from Table 3 that different wetting dispersants have obvious effects on the peeling force between the foam and the skin: Foam collapse occurs after the use of additive 2, which may be caused by excessive opening of the foam after the addition of additive 2; After the use of additives 1 and 3, the stripping strength of the blank sample has a certain increase, and the stripping strength of the additive 1 is about 17% higher than that of the blank sample, and the stripping strength of the additive 3 is about 25% higher than that of the blank sample. The difference between additive 1 and additive 3 is mainly caused by the difference in the wettability of the composite material on the surface. In general, to evaluate the wettability of liquid on solid, the contact Angle is an important parameter to measure the surface wettability. Therefore, the contact Angle between the composite material and the skin after adding the above two wetting dispersants was tested, and the results were shown in Figure 1.
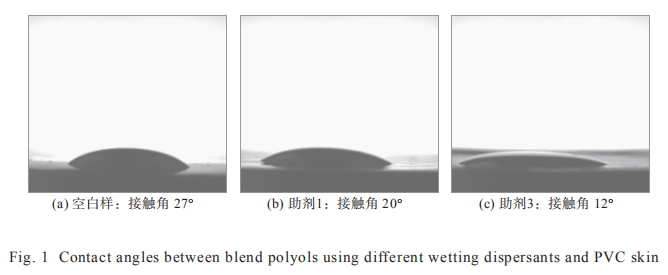
It can be seen from Figure 1 that the contact Angle of blank sample is the largest, which is 27°, and the contact Angle of auxiliary agent 3 is the smallest, which is only 12°. This shows that the use of additive 3 can improve the wettability of the composite material and the skin to a greater extent, and it is easier to spread on the surface of the skin, so the use of additive 3 has the greatest peeling force.
Aging property
Handrail products are pressed in the car, the frequency of sunlight exposure is high, and the aging performance is another important performance that polyurethane semi-rigid handrail foam has to consider. Therefore, the aging performance of the basic formula was tested and the improvement study was carried out, and the results were shown in Table 4.
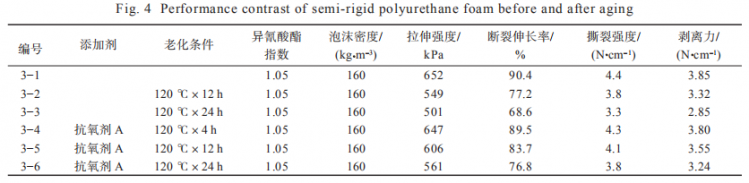
By comparing the data in Table 4, it can be found that the mechanical properties and bonding properties of the basic formula are significantly decreased after thermal aging at 120℃ : after aging for 12h, the loss of various properties except density (the same below) is 13%~16%; The performance loss of 24h aging is 23%~26%. It is indicated that the heat aging property of the basic formula is not good, and the heat aging property of the original formula can be obviously improved by adding A class of antioxidant A to the formula. Under the same experimental conditions after the addition of antioxidant A, the loss of various properties after 12h was 7%~8%, and the loss of various properties after 24h was 13%~16%. The decrease of mechanical properties is mainly due to a series of chain reactions triggered by chemical bond breakage and active free radicals during the thermal aging process, resulting in fundamental changes in the structure or properties of the original substance. On the one hand, the decline in bonding performance is due to the decline in the mechanical properties of the foam itself, on the other hand, because the PVC skin contains a large number of plasticizers, and the plasticizer migrates to the surface during the process of thermal oxygen aging. The addition of antioxidants can improve its thermal aging properties, mainly because antioxidants can eliminate newly generated free radicals, delay or inhibit the oxidation process of the polymer, so as to maintain the original properties of the polymer.
Comprehensive performance
Based on the above results, the optimal formula was designed and its various properties were evaluated. The performance of the formula was compared with that of the general polyurethane high rebound handrail foam. The results are shown in Table 5.

As can be seen from Table 5, the performance of the optimal semi-rigid polyurethane foam formula has certain advantages over the basic and general formulas, and it is more practical, and it is more suitable for the application of high-performance handrails.
Conclusion
Adjusting the amount of polyether and selecting qualified wetting dispersant and antioxidant can give the semi-rigid polyurethane foam good mechanical properties, excellent heat aging properties and so on. Based on the excellent performance of the foam, this high-performance polyurethane semi-rigid foam product can be applied to automotive buffer materials such as handrails and instrument tables.
Post time: Jul-25-2024