Research Progress on Non-Isocyanate Polyurethanes
Since their introduction in 1937, polyurethane (PU) materials have found extensive applications across various sectors including transportation, construction, petrochemicals, textiles, mechanical and electrical engineering, aerospace, healthcare, and agriculture. These materials are utilized in forms such as foam plastics, fibers, elastomers, waterproofing agents, synthetic leather, coatings, adhesives, paving materials and medical supplies. Traditional PU is primarily synthesized from two or more isocyanates along with macromolecular polyols and small molecular chain extenders. However, the inherent toxicity of isocyanates poses significant risks to human health and the environment; moreover they are typically derived from phosgene—a highly toxic precursor—and corresponding amine raw materials.
In light of the contemporary chemical industry's pursuit of green and sustainable development practices, researchers are increasingly focused on substituting isocyanates with environmentally friendly resources while exploring novel synthesis routes for non-isocyanate polyurethanes (NIPU). This paper introduces the preparation pathways for NIPU while reviewing advancements in various types of NIPUs and discussing their future prospects to provide a reference for further research.
1 Synthesis of Non-Isocyanate Polyurethanes
The first synthesis of low molecular weight carbamate compounds using monocyclic carbonates combined with aliphatic diamines occurred abroad in the 1950s—marking a pivotal moment towards non-isocyanate polyurethane synthesis. Currently there exist two primary methodologies for producing NIPU: The first involves stepwise addition reactions between binary cyclic carbonates and binary amines; the second entails polycondensation reactions involving diurethane intermediates alongside diols that facilitate structural exchanges within carbamates. Diamarboxylate intermediates can be obtained through either cyclic carbonate or dimethyl carbonate (DMC) routes; fundamentally all methods react via carbonic acid groups yielding carbamate functionalities.
The following sections elaborate on three distinct approaches to synthesizing polyurethane without utilizing isocyanate.
1.1Binary Cyclic Carbonate Route
NIPU can be synthesized through stepwise additions involving binary cyclic carbonate coupled with binary amine as illustrated in Figure 1.
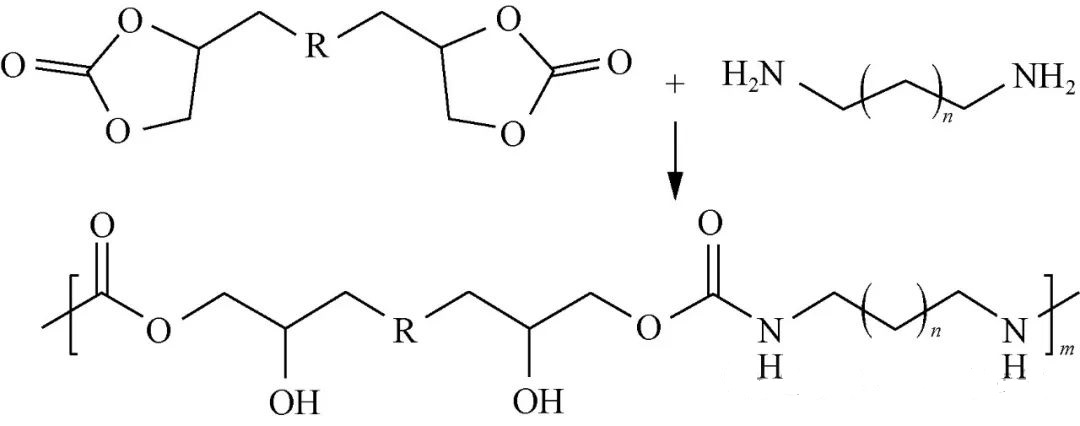
Due to multiple hydroxyl groups present within repeating units along its main chain structure this method generally yields what is termed polyβ-hydroxyl polyurethane (PHU). Leitsch et al., developed a series of polyether PHUs employing cyclic carbonate-terminated polyethers alongside binary amines plus small molecules derived from binary cyclic carbonates—comparing these against traditional methods used for preparing polyether PUs. Their findings indicated that hydroxyl groups within PHUs readily form hydrogen bonds with nitrogen/oxygen atoms located within soft/hard segments; variations among soft segments also influence hydrogen bonding behavior as well as microphase separation degrees which subsequently affect overall performance characteristics.
Typically conducted below temperatures exceeding 100 °C this route generates no by-products during reaction processes making it relatively insensitive toward moisture whilst yielding stable products devoid of volatility concerns however necessitating organic solvents characterized by strong polarity such as dimethyl sulfoxide (DMSO), N,N-dimethylformamide (DMF), etc.. Additionally extended reaction times ranging anywhere between one day up until five days often yield lower molecular weights frequently falling short beneath thresholds around 30k g/mol rendering large-scale production challenging due largely attributed both high costs associated therein coupled insufficient strength exhibited by resultant PHUs despite promising applications spanning damping material domains shape memory constructs adhesive formulations coating solutions foams etc..
1.2Monocylic Carbonate Route
Monocylic carbonate reacts directly with diamine resulting dicarbamate possessing hydroxyl end-groups which then undergoes specialized transesterification/polycondensation interactions alongside diols ultimately generating an NIPU structurally akin traditional counterparts depicted visually via Figure 2.
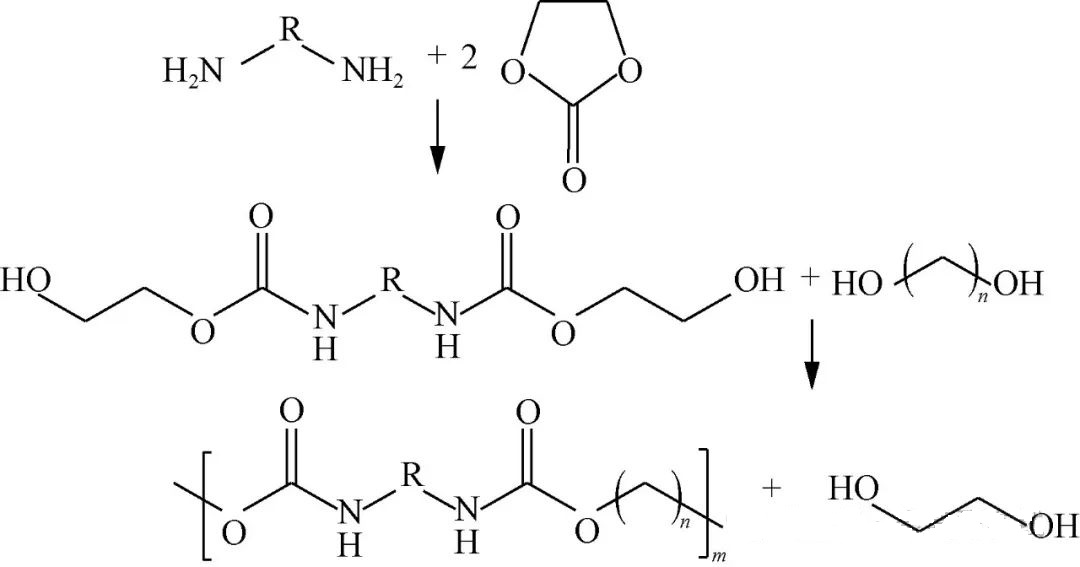
Commonly employed monocylic variants include ethylene & propylene carbonated substrates wherein Zhao Jingbo’s team at Beijing University Of Chemical Technology engaged diverse diamines reacting them against said cyclical entities initially obtaining varied structural dicarbamate intermediaries before proceeding onto condensation phases utilizing either polytetrahydrofuranediol/polyether-diols culminating successful formation respective product lines exhibiting impressive thermal/mechanical properties reaching upwards melting points hovering around range extending approximately125~161°C tensile strengths peaking near24MPa elongation rates nearing1476%. Wang et al., similarly leveraged combinations comprising DMC paired respectively w/hexamethylenediamine/cyclocarbonated precursors synthesizing hydroxy-terminated derivatives later subjected biobased dibasic acids like oxalic/sebacic/acids adipic-acid-terephtalics achieving final outputs showcasing ranges encompassing13k~28k g/mol tensile strengths fluctuating9~17 MPa elongations varying35%~235%.
Cyclocarbonic esters engage effectively without requiring catalysts under typical conditions maintaining temperature spans roughly80°to120°C subsequent transesterifications usually employ organotin-based catalytic systems ensuring optimal processing not surpassing200°. Beyond mere condensation efforts targeting diolic inputs capable self-polymerization/deglycolysis phenomena facilitating generation desired outcomes renders methodology inherently eco-friendly predominantly yielding methanol/small-molecule-diolic residues thus presenting viable industrial alternatives moving forward.
1.3Dimethyl Carbonate Route
DMC represents an ecologically sound/non-toxic alternative featuring numerous active functional moieties inclusive methyl/methoxy/carbonyl configurations enhancing reactivity profiles significantly enabling initial engagements whereby DMC interacts directly w/diamines forming smaller methyl-carbamate terminated intermediaries followed thereafter melt-condensing actions incorporating additional small-chain-extender-diolics/larger-polyol constituents leading eventual emergence sought-after polymer structures visualized accordingly via Figure3.
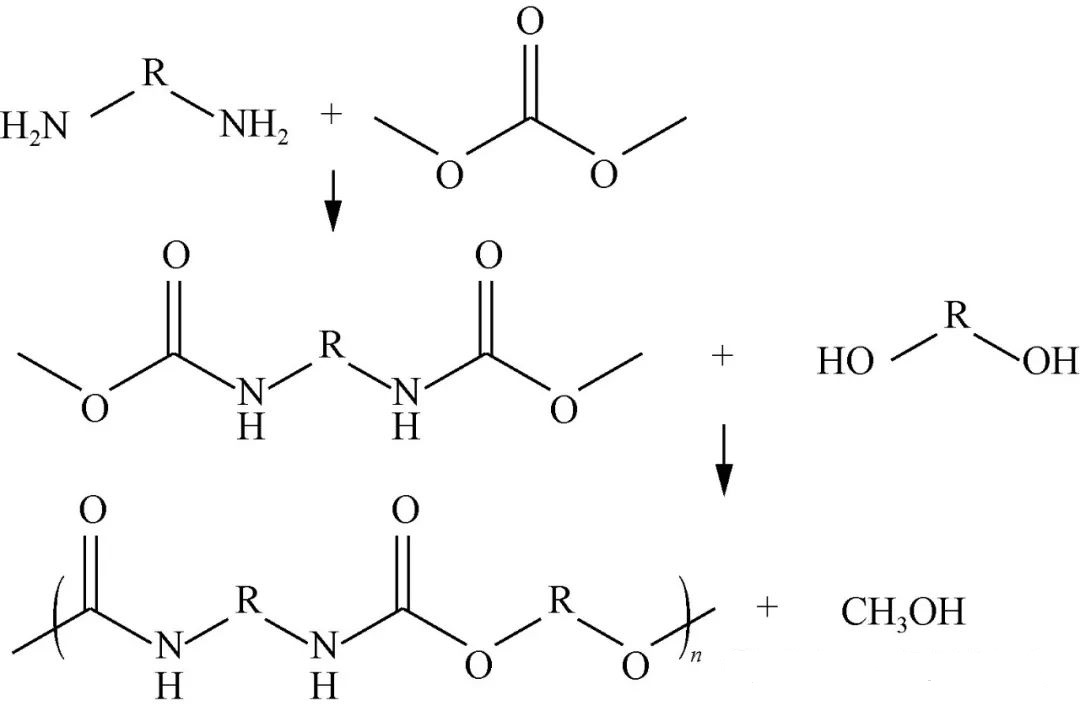
Deepa et.al capitalized upon aforementioned dynamics leveraging sodium methoxide catalysis orchestrating diverse intermediate formations subsequently engaging targeted extensions culminating series equivalent hard-segment compositions attaining molecular weights approximating(3 ~20)x10^3g/mol glass transition temperatures spanning(-30 ~120°C). Pan Dongdong selected strategic pairings consisting DMC hexamethylene-diaminopolycarbonate-polyalcohols realizing noteworthy results manifesting tensile-strength metrics oscillating10-15MPa elongation ratios approaching1000%-1400%. Investigative pursuits surrounding differing chain-extending influences revealed preferences favorably aligning butanediol/ hexanediol selections when atomic-number parity maintained evenness promoting ordered crystallinity enhancements observed throughout chains.Sarazin's group prepared composites integrating lignin/DMC alongside hexahydroxyamine demonstrating satisfactory mechanical attributes post-processing at230℃ .Additional explorations aimed deriving non-isocyante-polyureas leveraging diazomonomer engagement anticipated potential paint applications emerging comparative advantages over vinyl-carbonaceous counterparts highlighting cost-effectiveness/wider sourcing avenues available.Due diligence regarding bulk-synthesized methodologies typically necessitate elevated-temperature/vacuum environments negating solvent requirements thereby minimizing waste streams predominantly limited solely methanol/small-molecule-diolic effluents establishing greener syntheses paradigms overall.
2 Different soft segments of non-isocyanate polyurethane
2.1 Polyether polyurethane
Polyether polyurethane (PEU) is widely used because of its low cohesion energy of ether bonds in soft segment repeat units, easy rotation, excellent low temperature flexibility and hydrolysis resistance.
Kebir et al. synthesized polyether polyurethane with DMC, polyethylene glycol and butanediol as raw materials, but the molecular weight was low (7 500 ~ 14 800g/mol),Tg was lower than 0℃, and the melting point was also low (38 ~ 48℃), and the strength and other indicators were difficult to meet the needs of use. Zhao Jingbo's research group used ethylene carbonate, 1, 6-hexanediamine and polyethylene glycol to synthesize PEU, which has a molecular weight of 31 000g/mol, tensile strength of 5 ~ 24MPa, and elongation at break of 0.9% ~ 1 388%. The molecular weight of the synthesized series of aromatic polyurethanes is 17 300 ~ 21 000g/mol, the Tg is -19 ~ 10℃, the melting point is 102 ~ 110℃, the tensile strength is 12 ~ 38MPa, and the elastic recovery rate of 200% constant elongation is 69% ~ 89%.
The research group of Zheng Liuchun and Li Chuncheng prepared the intermediate 1, 6-hexamethylenediamine (BHC) with dimethyl carbonate and 1, 6-hexamethylenediamine, and polycondensation with different small molecules straight chain diols and polytetrahydrofuranediols (Mn=2 000). A series of polyether polyurethanes (NIPEU) with non-isocyanate route were prepared, and the crosslinking problem of intermediates during the reaction was solved. The structure and properties of traditional polyether polyurethane (HDIPU) prepared by NIPEU and 1, 6-hexamethylene diisocyanate were compared, as shown in Table 1.
Sample | Hard segment mass fraction/% | Molecular weight/(g·mol^(-1)) | Molecular weight distribution index | Tensile strength/MPa | Elongation at break/% |
NIPEU30 | 30 | 74000 | 1.9 | 12.5 | 1250 |
NIPEU40 | 40 | 66000 | 2.2 | 8.0 | 550 |
HDIPU30 | 30 | 46000 | 1.9 | 31.3 | 1440 |
HDIPU40 | 40 | 54000 | 2.0 | 25.8 | 1360 |
Table 1
The results in Table 1 show that the structural differences between NIPEU and HDIPU are mainly due to the hard segment. The urea group generated by the side reaction of NIPEU is randomly embedded in the hard segment molecular chain, breaking the hard segment to form ordered hydrogen bonds, resulting in weak hydrogen bonds between the molecular chains of the hard segment and low crystallinity of the hard segment, resulting in low phase separation of NIPEU. As a result, its mechanical properties are much worse than HDIPU.
2.2 Polyester Polyurethane
Polyester polyurethane (PETU) with polyester diols as soft segments has good biodegradability, biocompatibility and mechanical properties, and can be used to prepare tissue engineering scaffolds, which is a biomedical material with great application prospects. Polyester diols commonly used in soft segments are polybutylene adipate diol, polyglycol adipate diol and polycaprolactone diol.
Earlier, Rokicki et al. reacted ethylene carbonate with diamine and different diols (1, 6-hexanediol,1, 10-n-dodecanol) to obtain different NIPU, but the synthesized NIPU had lower molecular weight and lower Tg. Farhadian et al. prepared polycyclic carbonate using sunflower seed oil as raw material, then mixed with bio-based polyamines, coated on a plate, and cured at 90 ℃ for 24 h to obtain thermosetting polyester polyurethane film, which showed good thermal stability. The research group of Zhang Liqun from South China University of Technology synthesized a series of diamines and cyclic carbonates, and then condensed with biobased dibasic acid to obtain biobased polyester polyurethane. Zhu Jin's research group at Ningbo Institute of Materials Research, Chinese Academy of Sciences prepared diaminodiol hard segment using hexadiamine and vinyl carbonate, and then polycondensation with bio-based unsaturated dibasic acid to obtain a series of polyester polyurethane, which can be used as paint after ultraviolet curing [23]. The research group of Zheng Liuchun and Li Chuncheng used adipic acid and four aliphatic diols (butanediol, hexadiol, octanediol and decanediol) with different carbon atomic numbers to prepare the corresponding polyester diols as soft segments; A group of non-isocyanate polyester polyurethane (PETU), named after the number of carbon atoms of aliphatic diols, was obtained by melting polycondensation with the hydroxy-sealed hard segment prepolymer prepared by BHC and diols. The mechanical properties of PETU are shown in Table 2.
Sample | Tensile strength/MPa | Elastic modulus/MPa | Elongation at break/% |
PETU4 | 6.9±1.0 | 36±8 | 673±35 |
PETU6 | 10.1±1.0 | 55±4 | 568±32 |
PETU8 | 9.0±0.8 | 47±4 | 551±25 |
PETU10 | 8.8±0.1 | 52±5 | 137±23 |
Table 2
The results show that the soft segment of PETU4 has the highest carbonyl density, the strongest hydrogen bond with the hard segment, and the lowest phase separation degree. The crystallization of both the soft and hard segments is limited, showing low melting point and tensile strength, but the highest elongation at break.
2.3 Polycarbonate polyurethane
Polycarbonate polyurethane (PCU), especially aliphatic PCU, has excellent hydrolysis resistance, oxidation resistance, good biological stability and biocompatibility, and has good application prospects in the field of biomedicine. At present, most of the prepared NIPU uses polyether polyols and polyester polyols as soft segments, and there are few research reports on polycarbonate polyurethane.
The non-isocyanate polycarbonate polyurethane prepared by Tian Hengshui's research group at South China University of Technology has a molecular weight of more than 50 000 g/mol. The influence of reaction conditions on the molecular weight of the polymer has been studied, but its mechanical properties have not been reported. Zheng Liuchun and Li Chuncheng's research group prepared PCU using DMC, hexanediamine, hexadiol and polycarbonate diols, and named PCU according to the mass fraction of the hard segment repeating unit. The mechanical properties are shown in Table 3.
Sample | Tensile strength/MPa | Elastic modulus/MPa | Elongation at break/% |
PCU18 | 17±1 | 36±8 | 665±24 |
PCU33 | 19±1 | 107±9 | 656±33 |
PCU46 | 21±1 | 150±16 | 407±23 |
PCU57 | 22±2 | 210±17 | 262±27 |
PCU67 | 27±2 | 400±13 | 63±5 |
PCU82 | 29±1 | 518±34 | 26±5 |
Table 3
The results show that PCU has high molecular weight, up to 6×104 ~ 9×104g/mol, melting point up to 137 ℃, and tensile strength up to 29 MPa. This kind of PCU can be used either as a rigid plastic or as an elastomer, which has a good application prospect in the biomedical field (such as human tissue engineering scaffolds or cardiovascular implant materials).
2.4 Hybrid non-isocyanate polyurethane
Hybrid non-isocyanate polyurethane (hybrid NIPU) is the introduction of epoxy resin, acrylate, silica or siloxane groups into the polyurethane molecular framework to form an interpenetrating network, improve the performance of the polyurethane or give the polyurethane different functions.
Feng Yuelan et al. reacted bio-based epoxy soybean oil with CO2 to synthesize pentamonic cyclic carbonate (CSBO), and introduced bisphenol A diglycidyl ether (epoxy resin E51) with more rigid chain segments to further improve the NIPU formed by CSBO solidified with amine. The molecular chain contains a long flexible chain segment of oleic acid/linoleic acid. It also contains more rigid chain segments, so that it has high mechanical strength and high toughness. Some researchers also synthesized three kinds of NIPU prepolymers with furan end groups through the rate-opening reaction of diethylene glycol bicyclic carbonate and diamine, and then reacted with unsaturated polyester to prepare a soft polyurethane with self-healing function, and successfully realized the high self-healing efficiency of soft NIPU. Hybrid NIPU not only has the characteristics of general NIPU, but also may have better adhesion, acid and alkali corrosion resistance, solvent resistance and mechanical strength.
3 Outlook
NIPU is prepared without the use of toxic isocyanate, and is currently being studied in the form of foam, coating, adhesive, elastomer and other products, and has a wide range of application prospects. However, most of them are still limited to laboratory research, and there is no large-scale production. In addition, with the improvement of people's living standards and the continuous growth of demand, NIPU with a single function or multiple functions has become an important research direction, such as antibacterial, self-repair, shape memory, flame retardant, high heat resistance and so on. Therefore, the future research should grasp how to break through the key problems of industrialization and continue to explore the direction of preparing functional NIPU.
Post time: Aug-29-2024