Technical Aspects of Rigid Foam Polyurethane Field Spraying
Rigid foam polyurethane (PU) insulation material is a polymer with a repetitive structure unit of carbamate segment, formed by the reaction of isocyanate and polyol. Due to its excellent thermal insulation and waterproof performance, it finds wide applications in external wall and roof insulation, as well as in cold storage, grain storage facilities, archive rooms, pipelines, doors, windows and other specialized thermal insulation areas.
Currently, apart from roofing insulation and waterproofing applications, it also serves various purposes such as cold storage facilities and large to medium-sized chemical installations.
Key technology for rigid foam polyurethane spray construction
The mastery of rigid foam polyurethane spraying technology poses challenges due to potential issues like uneven foam holes. It is essential to enhance the training of construction personnel so that they can proficiently handle spraying techniques and independently resolve technical problems encountered during construction. The primary technical challenges in spraying construction are mainly focused on the following aspects:
Control over whitening time and atomization effect.
The formation of polyurethane foam involves two stages: foaming and curing.
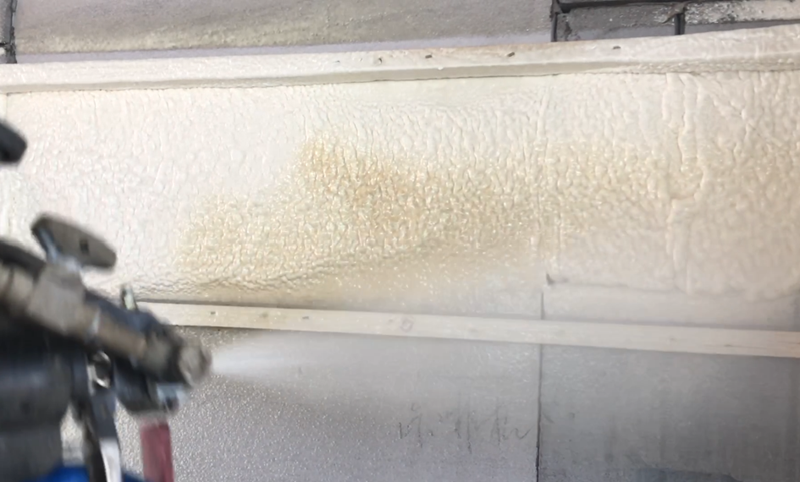
From the mixing stage until the expansion of foam volume ceases - this process is known as foaming. During this phase, uniformity in bubble hole distribution should be considered when a substantial amount of reactive hot ester is released into the system during spraying operations. Bubble uniformity primarily depends on factors such as:
1. Material ratio deviation
There exists significant density variation between machine-generated bubbles versus manually generated ones. Typically, machine-fixed material ratios are 1:1; however due to varying viscosity levels among different manufacturers' white materials - actual material ratios may not align with these fixed ratios leading to discrepancies in foam density based on excessive white or black material usage.
2.Ambient temperature
Polyurethane foams are highly sensitive to temperature fluctuations; their foaming process relies heavily on heat availability which comes from both chemical reactions within the system itself along with environmental provisions.
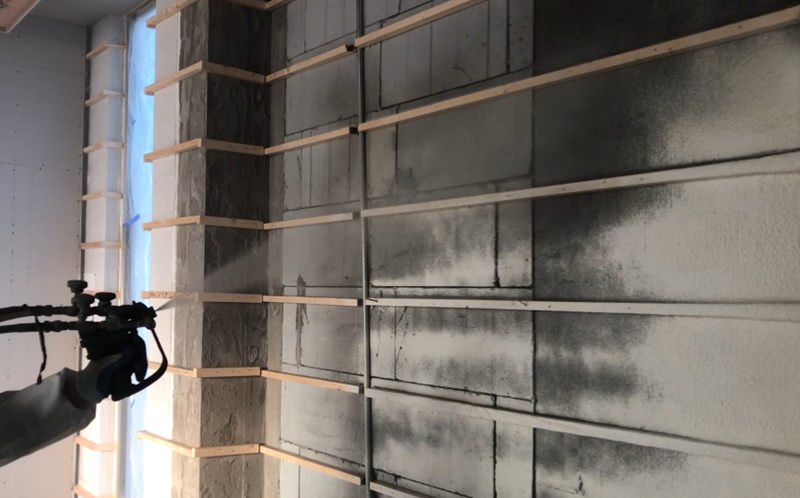
When ambient temperatures are high enough for environmental heat provision - it accelerates reaction speed resulting in fully expanded foams with consistent surface-to-core densities.
Conversely at lower temperatures (e.g., below 18°C), some reaction heat dissipates into surroundings causing prolonged curing periods alongside increased molding shrinkage rates thereby elevating production costs.
3.Wind
During spraying operations wind speeds should ideally remain below 5m/s; exceeding this threshold blows away reaction-generated heat affecting rapid foaming while making product surfaces brittle.
4.Base temperature & humidity
Base wall temperatures significantly influence polyurethane's foaming efficiency during application processes especially if ambient & base wall temps are low – quick absorption occurs after initial coating reducing overall material yield.
Therefore minimizing noon rest times during constructions alongside strategic scheduling arrangements becomes crucial for ensuring optimal rigid foam polyurethane expansion rates.
Rigid Polyurethane Foam represents a polymer product formed through reactions between two components – Isocyanate & combined Polyether.
Isocyanate components readily react with water producing urea bonds; an increase in urea bond content renders resulting foams brittle while decreasing adhesion between them & substrates hence necessitating clean dry substrate surfaces free from rust/dust/moisture/pollution particularly avoiding rainy days where dew/frost presence requires removal followed by drying before proceeding further.
Post time: Jul-16-2024